How to Strengthen Sticker Adhesion: Causes of Peeling and Solutions
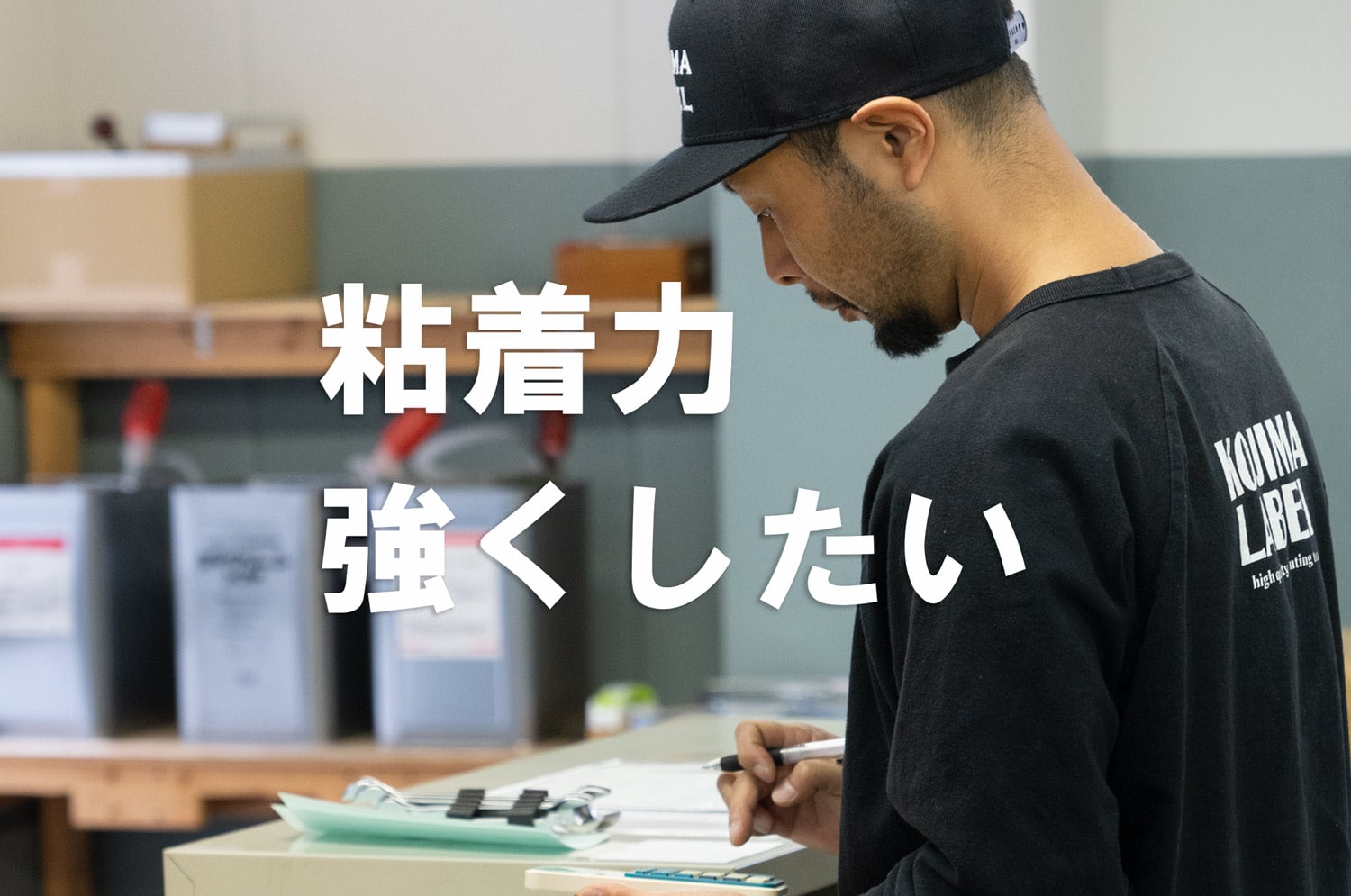
The adhesive strength of a sticker is determined by the type of adhesive used. When applying to surfaces with high loads or in situations where peeling would be problematic, it is important to choose a high-strength adhesive from the start.
Also, depending on the intended use, if an unsuitable adhesive is used, the sticker may peel off. This article explains the various types and characteristics of adhesives that help ensure your stickers last longer.
We carefully listen to your sticker requirements and usage scenarios, and then propose the most suitable materials and adhesives. If you wish to produce custom, high-performance stickers, please feel free to contact us.
For those struggling with label and sticker printing
Wondering if this kind of printing is possible? Or how much budget is needed?
If you have any concerns, feel free to reach out to us.
First, check out our case studies.
※Orders are available starting from 1,000 pieces.
※Business hours: Japan Standard Time, Monday to Friday, 9:00 AM - 5:00 PM
There Is No Way to Increase the Adhesive Strength of a Sticker
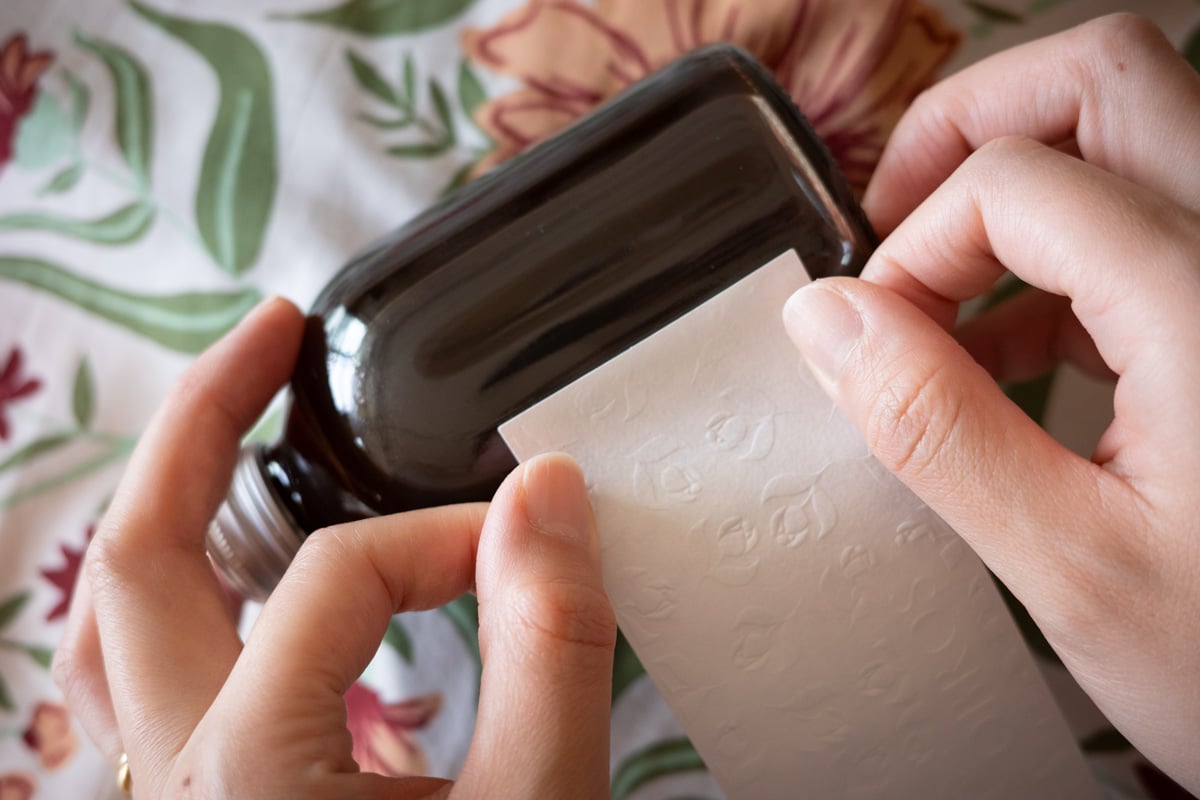
In short, there is no method to increase the adhesive strength of a completed sticker. The adhesive strength depends on the type of adhesive that was originally selected.
If you only want to prevent peeling, you might consider applying tape over it or using double-sided tape, but these options can spoil the appearance and are generally only suitable for personal use.
To avoid the mistake of needing stronger adhesion for a product sticker, it is crucial to choose the appropriate adhesive type for the intended use and application surface at the time of purchase.
We are a sticker printing company specializing in product labels. If you are looking for or want to know more about stickers with the optimal adhesive strength, please feel free to contact us via “Contact Us”.
Also, the following article explains the characteristics of adhesives used in stickers by type, so please check it out as well.
Sticker Adhesion | All About the Optimal Adhesive Types for Your Business!
Three Special Adhesive Types That Resist Peeling
The following peel-resistant adhesive types are used when enhanced adhesive strength is required:
- High-adhesion / Ultra-high adhesion
- For Rough Surfaces (Toishi Type)
- Special Series
Type 1: High-Adhesion / Ultra-High Adhesion
The high-adhesion / ultra-high adhesion type is used when standard adhesives do not provide enough strength in demanding applications.
The following examples showcase stickers produced using high-adhesion adhesives.
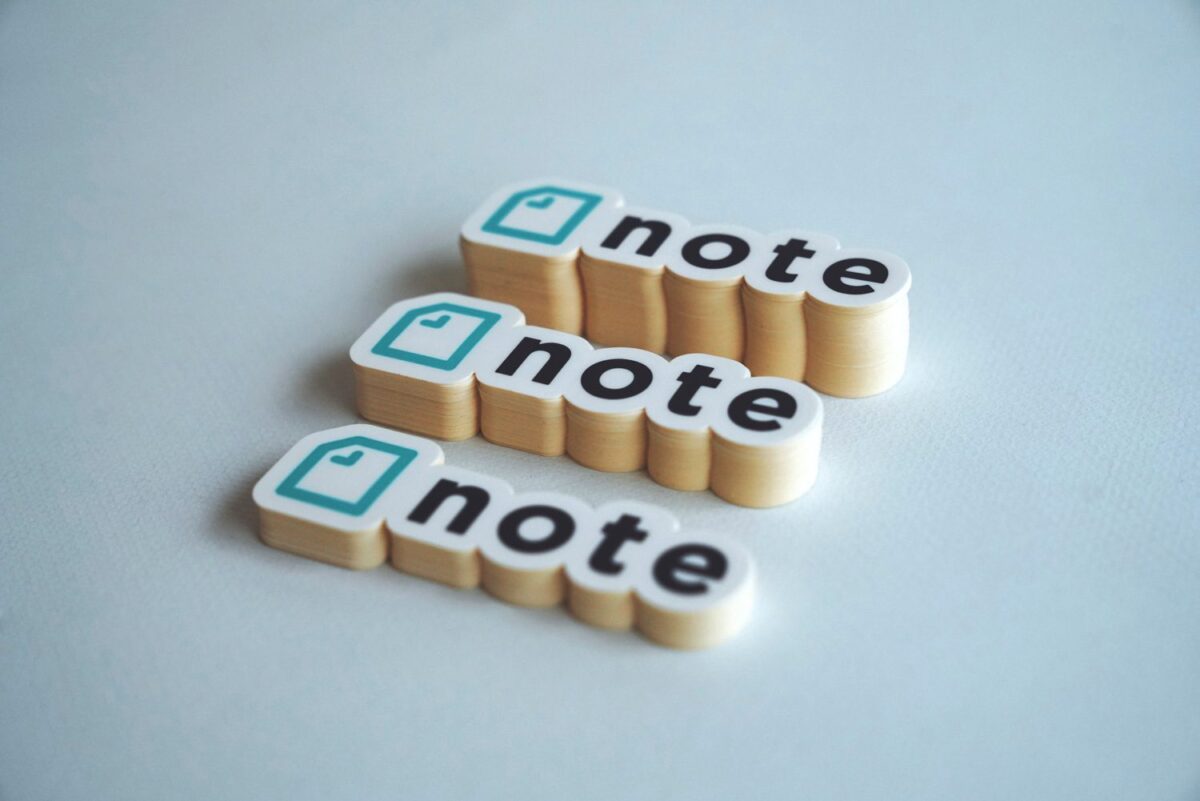
While standard adhesives work well under normal conditions, they may fail in high-stress situations.
For products used indoors, standard adhesives may suffice. However, for stickers used in abrasive or outdoor environments, it is necessary to opt for high-adhesion or ultra-high adhesion adhesives.
Type 2: For Rough Surfaces (Toishi Type)
The Toishi type is the adhesive with the highest strength, also known as the adhesive for rough surfaces. Stickers produced with this adhesive can adhere even to uneven surfaces.
This type is primarily used for industrial stickers and labels, and can be applied in situations where high-adhesion or ultra-high adhesion adhesives are insufficient. However, since it is very difficult to remove once applied, careful application is necessary.
The following is a production example using the Toishi type, which is the strongest adhesive used to ensure stickers do not peel off from pouch products.
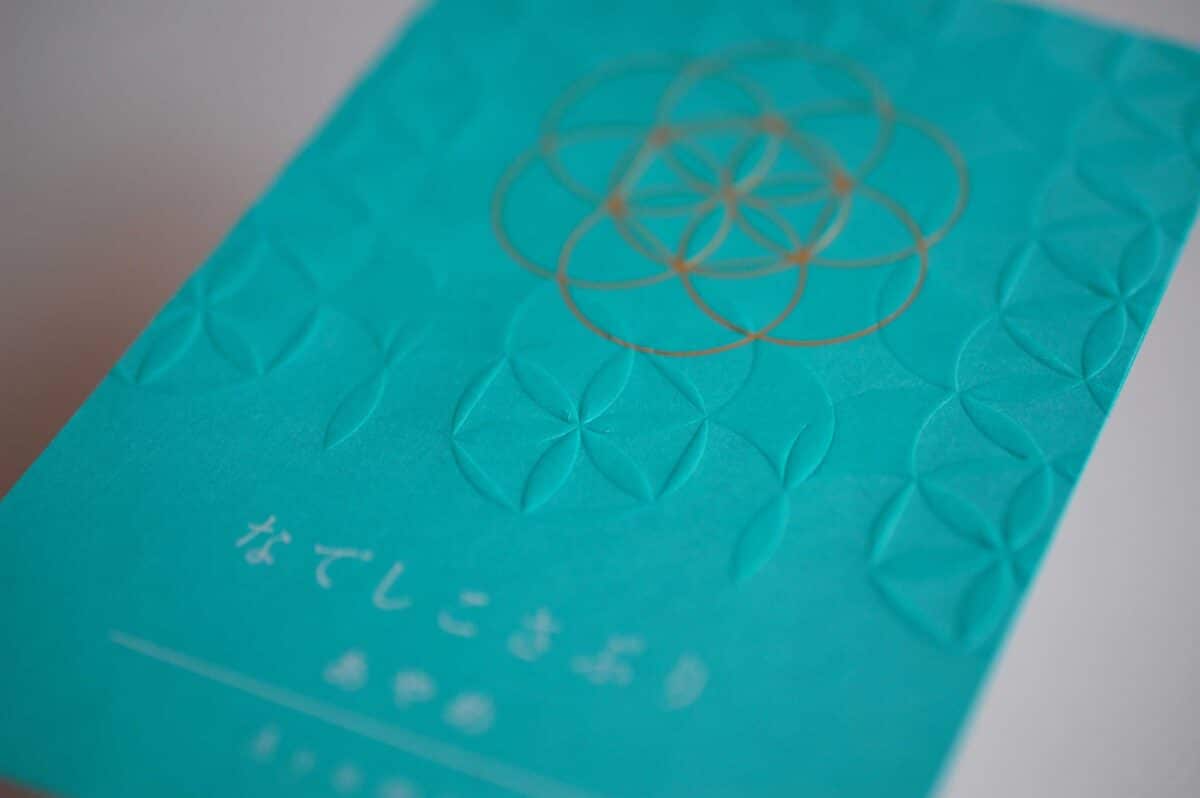
However, a stronger adhesive does not always guarantee better performance, so it is crucial to select the adhesive based on the specific environment in which it will be used.
Type 3: Special Series
This section introduces specialized adhesives designed for use in unique environments.
- For Refrigeration
- For Freezing
- For Ham Products
- For Oily Surfaces
The refrigeration type maintains its adhesive strength in environments ranging from 5°C to 15°C. It is recommended for use on refrigerated food products.
The freezing type is designed for environments between -5°C and 5°C. Using a standard adhesive in a freezer may cause it to harden, resulting in loss of stickiness. Always choose the appropriate adhesive for frozen food labels.
The characteristics of ham adhesives include resistance to low temperatures and the ability to adhere to uneven surfaces. This adhesive was specifically developed for ham that cannot be flattened by vacuum packaging.
The following is an example of a ham label sticker produced by our company.
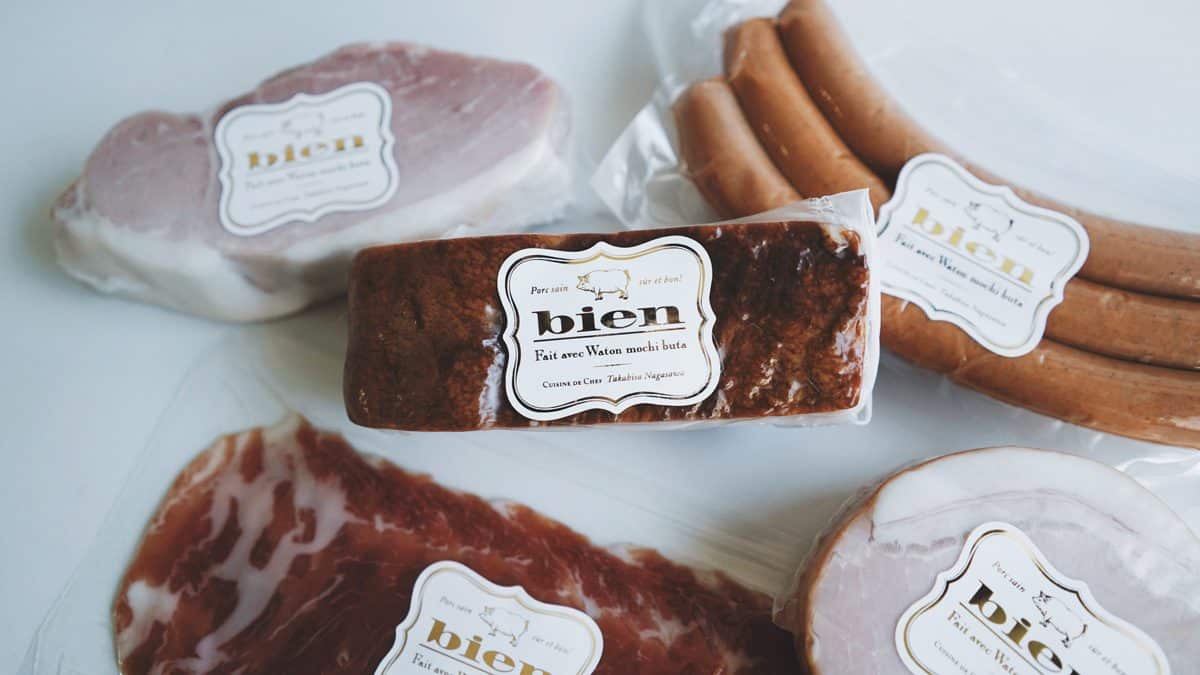
For oily surfaces, the adhesive is formulated to absorb oil, allowing the sticker to adhere even on greasy areas. Choosing the right adhesive for the usage scenario is key to enhancing both the adhesive strength and longevity of the sticker.
Features of Freeze-Proof Stickers! Differences from Standard Stickers and Production Examples
Three Common Causes of Sticker Peeling
There are several potential reasons why a sticker might peel, but the three most common causes are as follows:
- Applied to a surface that is prone to peeling
- Dirt on the application surface or adhesive area
- Not choosing the appropriate adhesive type for the intended use
Cause 1: Applied to a Surface That Is Prone to Peeling
Surfaces that are uneven or rough do not allow stickers to adhere well, causing them to peel off quickly. The main reason is that air becomes trapped between the uneven surface and the adhesive, reducing the contact area and making the sticker more susceptible to peeling.
To prevent peeling, it is important to choose a flat and smooth surface for application. If you know the environment is prone to peeling from the outset, you should select a high-adhesion adhesive suitable for that situation.
Cause 2: Dirt on the Application Surface or Adhesive Area
If the surface is dusty or has oil residues, the sticker will not adhere properly. Film materials, in particular, tend to generate static electricity, which attracts dust and particles, so caution is needed.
Moreover, if the surface is wet, the sticker will not stick well. Using adhesive tape or clothing cleaners to prevent dust or hair from transferring from your clothes can be effective. Pre-cleaning and drying the application area will improve the sticker’s adhesive strength and lifespan.
Cause 3: Not Choosing the Appropriate Adhesive Type for the Intended Use
Using a standard adhesive sticker in a low-temperature environment can result in weakened adhesion. Because adhesives are generally sensitive to cold, a standard sticker may peel off when placed in a refrigerator or freezer.
Similarly, if a sticker is used in a water-prone area, it is important to choose materials and adhesives with high water resistance. Selecting the right material and adhesive based on the environment is key to ensuring the sticker remains securely attached.
As a sticker printing company, we have produced numerous custom stickers. We can recommend the most suitable materials and adhesives based on your usage needs, so please feel free to contact us via “Contact Us”.
Types of Stickers That Require Enhanced Adhesive Strength
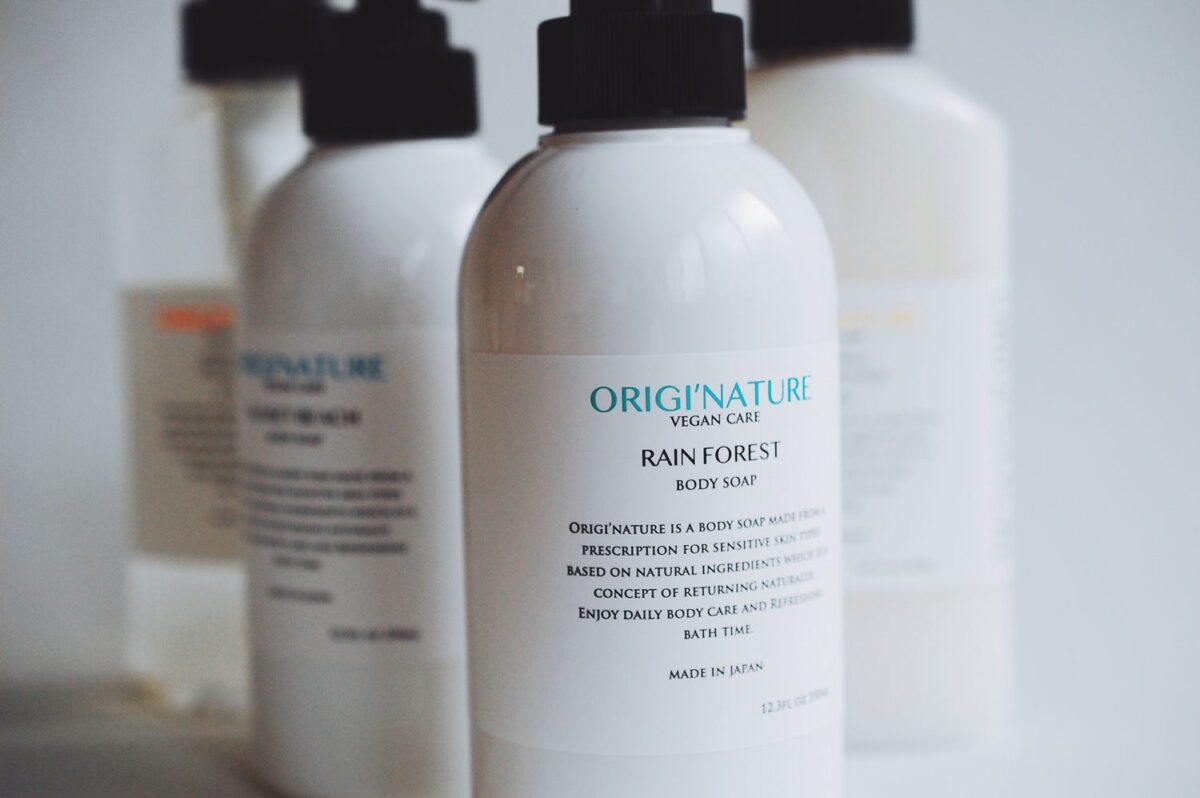
Unlike standard stickers, the following types require higher adhesive strength:
- Waterproof stickers
- Outdoor stickers
- Refrigerated / Frozen stickers
Type 1: Waterproof Stickers
Waterproof stickers are designed for use in environments where exposure to water is frequent. They are produced using water-resistant materials and adhesives to ensure that the printed content does not deteriorate.
Since paper materials are vulnerable to water, it is essential to choose film materials. Additionally, using adhesives with high water resistance will result in stickers that can be used in wet environments.
Adhesives are available in a range of options—from those with simply high adhesive strength to those that combine high adhesion with the ability to be repositioned. Please choose the adhesive type that best fits your purpose and usage.
How to Make Waterproof Stickers and Labels! Production Methods, Ordering Process, and Examples
Type 2: Outdoor Stickers
Outdoor stickers are exposed to wind, rain, and UV rays, which can cause them to deteriorate quickly. To enhance their durability, it is necessary to use high-adhesion adhesives and durable, water-resistant film materials.
However, even with these measures, UV exposure can cause fading of the printed content. For long-term outdoor use, we recommend applying a UV-cut laminate finish. This not only improves durability but also prevents degradation from sunlight, resulting in stickers that are robust and long-lasting.
Type 3: Refrigerated / Frozen Stickers
Since standard adhesives are sensitive to low temperatures, it is recommended to use specialized adhesives when producing stickers intended for products stored in refrigerators or freezers.
Stickers made with standard adhesives will naturally peel in low-temperature environments. Due to temperature fluctuations, such as when a door is opened, condensation may occur. Therefore, it is important to select materials and adhesives that are resistant to moisture. For stickers used on refrigerated or frozen products, choose those specifically designed for low temperatures and moisture exposure.
The following article explains how to select adhesives suitable for refrigerated and frozen products.
How to Make Food Labels? A Checklist and Tips for Creating Them
For Choosing the Right Adhesive for Your Product, Consultation with a Sticker Printing Company Is Recommended
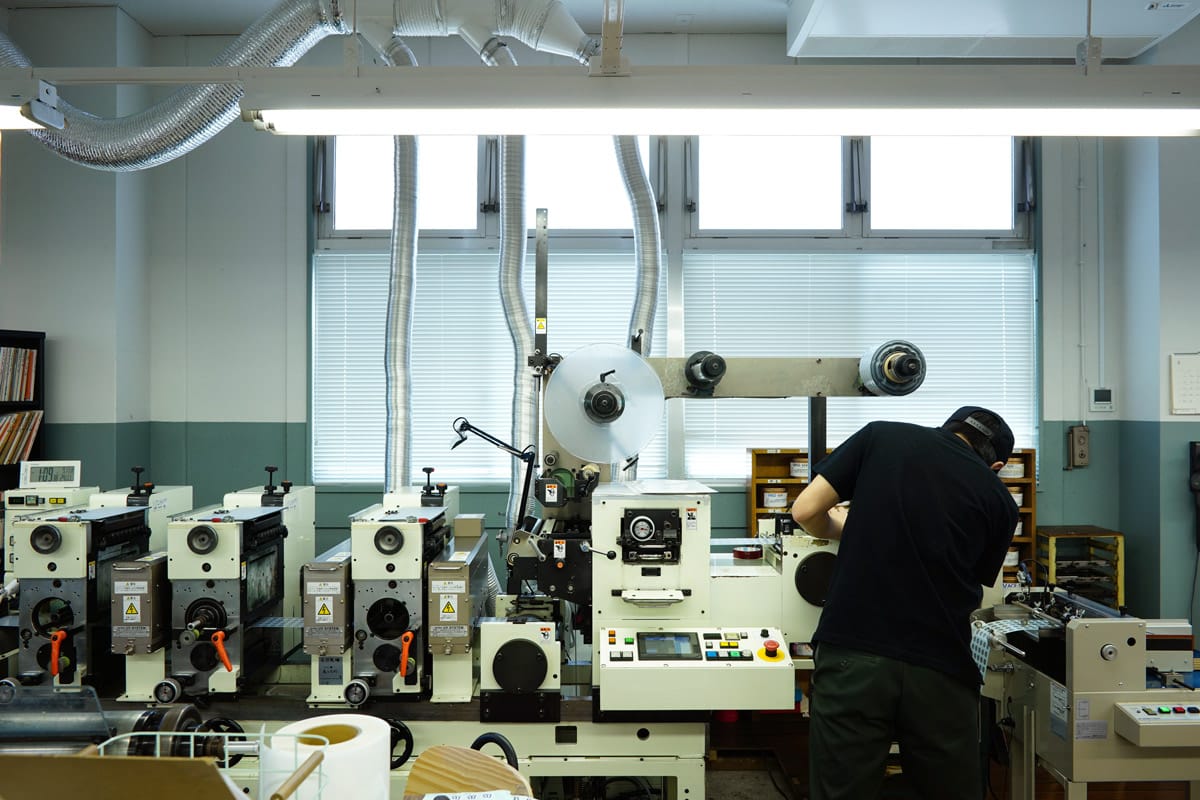
Essentially, the adhesive strength of a sticker is largely determined by the choice of adhesive from the start. Therefore, there is no way to simply increase the adhesive strength after production.
If you prioritize preventing stickers from peeling, it is important to select materials and adhesives that are appropriate for the intended environment and usage from the outset. Use the information in this article as a reference when selecting adhesives for your stickers.
We are a sticker printing company producing a wide range of stickers for various applications. If you want to emphasize not only design but also functionality tailored to your specific needs, please feel free to contact us.
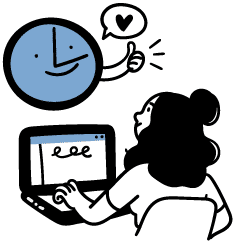
Start Your Project Now!
Contact Us or Get a Quote!