Types and Features of Lamination Processing: Water Resistance and Effects on Stickers
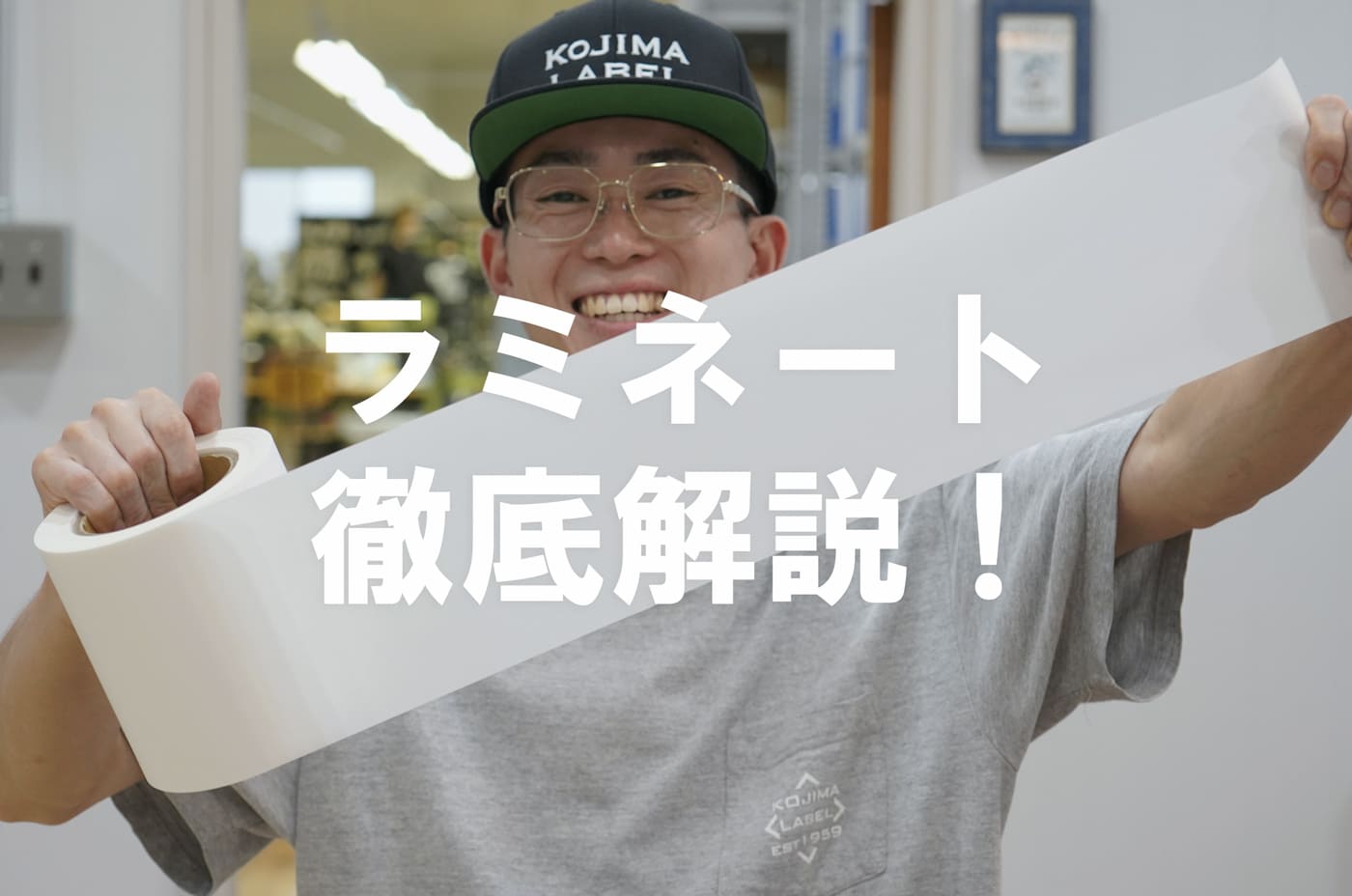
Seals are items used in a variety of scenes both indoors and outdoors and are often affixed for long periods. However, depending on the material and environment, there is sometimes a need to enhance durability. This is where lamination becomes invaluable.
Lamination protects the printed surface and improves water resistance and durability, thereby enhancing the strength of the seal. Additionally, the texture of the film adds to its visual appeal, which is another advantage of lamination.
When producing seals at our company, we carefully listen to our customers’ intended usage and desired final image, and then propose the most suitable materials and processing methods. Please feel free to contact us for quotations or inquiries.
For those struggling with label and sticker printing
Wondering if this kind of printing is possible? Or how much budget is needed?
If you have any concerns, feel free to reach out to us.
First, check out our case studies.
※Orders are available starting from 1,000 pieces.
※Business hours: Japan Standard Time, Monday to Friday, 9:00 AM - 5:00 PM
Features of Laminating Seals and Stickers
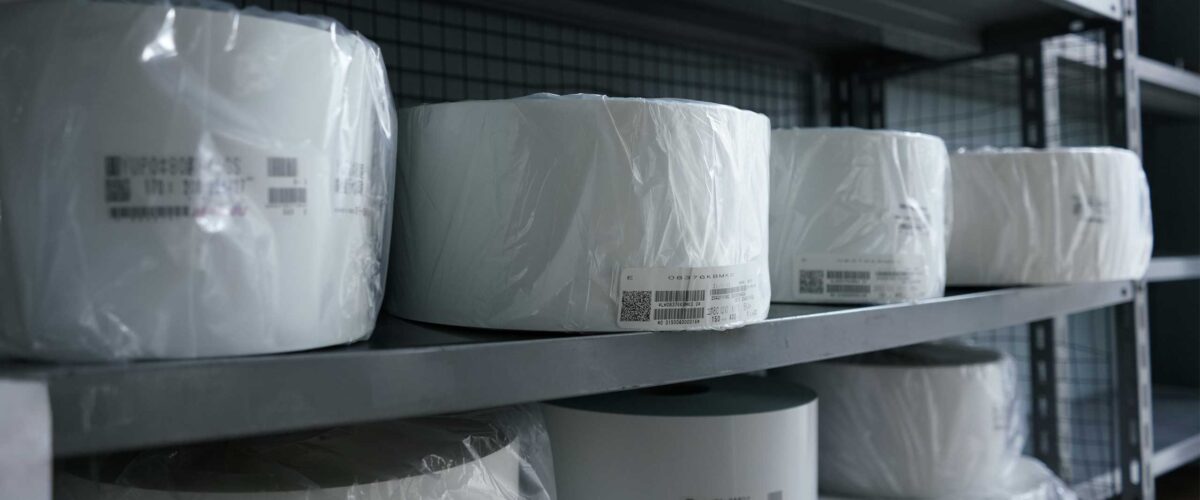
Lamination is the process of applying a transparent film to the surface of a seal. It provides a glossy or matte finish effect on the seal's surface and also serves to protect the printed surface.
The selection of film materials is as shown in the table below.
Material | Usage |
PP (Polypropylene) | For indoor use |
PET (Polyester) | For outdoor use |
With UV Cut Function | For long-term outdoor use |
If the surface is smooth, virtually any material can be laminated. However, materials that are not coated, such as fine paper, craft paper, or traditional Japanese paper, are not well-suited for lamination. In fact, the inherent texture may be compromised by lamination, so it is not recommended.
This may be confusing for non-experts, but it is important to use lamination with the appropriate materials and in the right situations.
There Are Mainly Two Options for Lamination Processing
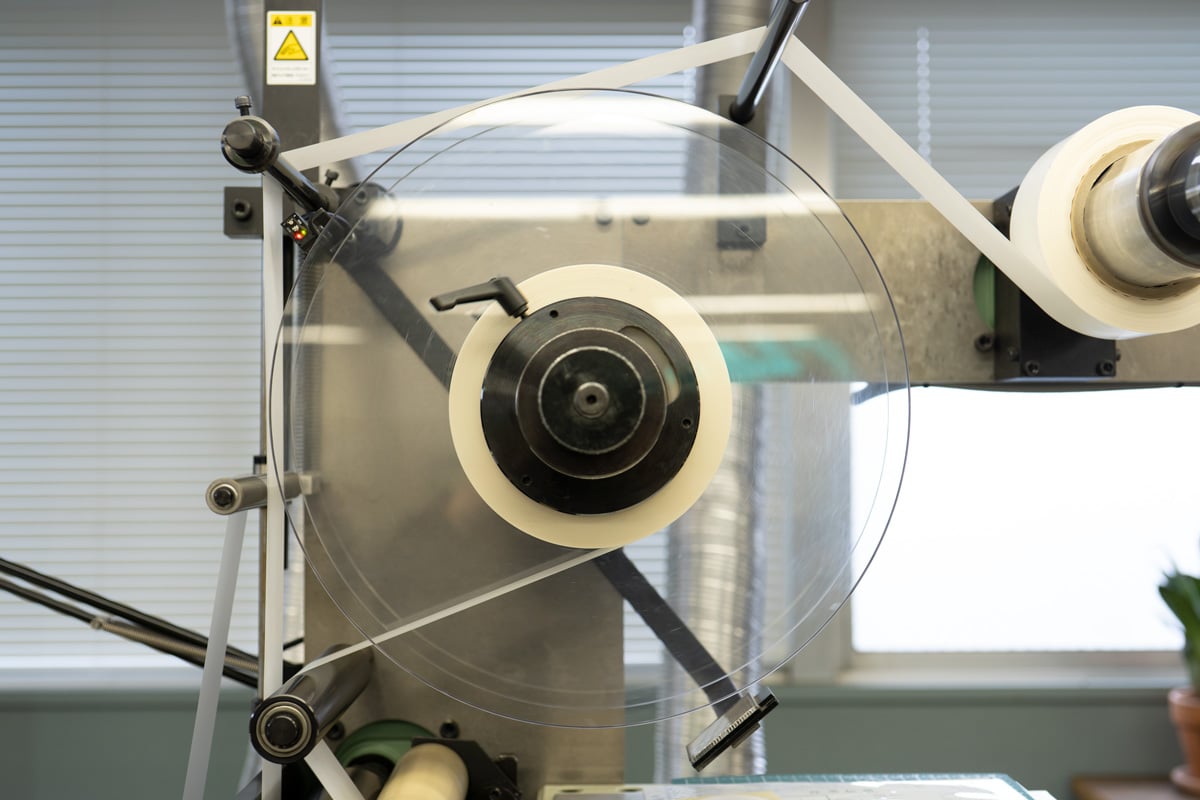
There are two types of lamination processes.
- Glossy Lamination
- Matte Lamination
Type 1: Glossy Lamination
Glossy lamination uses a film material with a glossy finish. It gives the printed surface a radiant shine and enhances the vibrancy of colors.
It can also enhance the contrast in photos and illustrations, making it versatile for printed materials and advertisements. When used on seals, it is recommended for situations where you want to reflect light to make the seal stand out or achieve a dazzling finish.
Type 2: Matte Lamination
Matte lamination uses a film material without gloss. Although the printed image may appear slightly subdued due to the semi-transparent film, it significantly increases the sense of luxury. It reduces light reflection for a subdued appearance and offers a smooth texture, which are its distinguishing features.
Since it does not reflect light even under bright illumination, it is ideal for seals that include text. While it may not have the flamboyance of glossy lamination, it is recommended when a chic and luxurious look is desired. It gives an impression similar to that of an iPhone box. Among our clients, matte lamination is particularly popular.
Bonus: UV-Cut Lamination
UV-cut lamination processing reduces the ultraviolet rays that cause ink fading.
The reason outdoor printed materials are prone to fading is due to the ultraviolet rays from sunlight. UV-cut laminate films contain UV absorbers that reduce the amount of UV reaching the surface, thereby extending the lifespan of the printed material. However, the UV-cut effect is not extreme; it only slightly outlasts other types of lamination. We recommend silk printing, which uses a high ink density, depending on the color. If you would like to learn more about silk printing, please see the article below. What is Silk Printing? Explaining the Differences and Process Compared to Other Methods
Three Benefits of Laminating Seals and Stickers
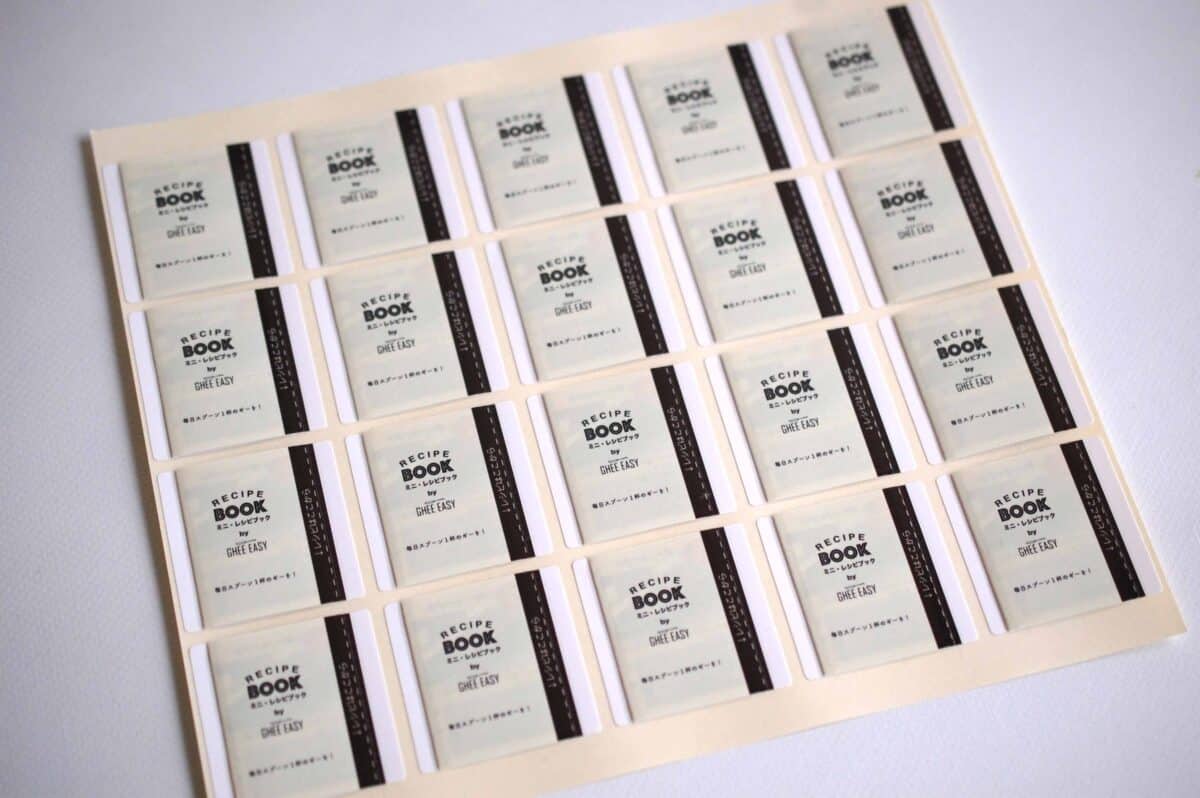
The expected benefits of applying lamination to seals and stickers are as follows:
- Improved water resistance and durability
- Enhanced appearance and a luxurious feel
- Added strength suitable for outdoor use
Effect 1: Improved Water Resistance and Durability
Lamination protects the surface of seals, enhancing their water resistance and durability. PP (Polypropylene) and PET (Polyester) used in the process are highly water-repellent and wear-resistant, making them excellent for waterproofing and anti-fouling.
In addition, lamination mitigates physical impacts from external sources, helping to prevent wear of the printed surface. Although paper materials cannot be made completely waterproof, their water resistance and durability are significantly improved compared to before lamination.
Effect 2: Enhanced Appearance and a Luxurious Feel
Laminated film improves the look of the printed surface and creates a luxurious appearance. Depending on the type of film, for instance, glossy lamination is effective when a shiny finish is desired.
On the other hand, matte lamination has an anti-glare effect, making it ideal for achieving a subdued look. Since both types of film protect the printed surface, lamination is recommended even for seals that are used over long periods.
Effect 3: Added Strength for Outdoor Use
Using a UV-cut laminate film makes the seal less prone to degradation from sunlight, allowing it to be used outdoors.
Outdoors, where seals are continuously exposed to sunlight and weather conditions such as wind and rain, significantly higher durability is required compared to indoor use. Unlaminated seals and stickers are vulnerable to UV rays, which accelerates their degradation over time. Even if the material is highly water-resistant, without a protective film, it is difficult to prevent ink deterioration.
By using a laminate film with a UV-cut effect, not only is water resistance and durability improved, but the printed surface is also protected from UV rays.
Our company produces seals for a wide range of applications, from standard types to those used in outdoor and wet environments. If you have any questions, please feel free to contact us via our inquiries page.
Same Day Service is available. Please give it a try.
Precautions When Laminating Seals and Stickers
The precautions when applying lamination to seals are as follows:
- The texture and color rendition of the printed surface may change
- Some materials are not suitable for lamination
- Paper materials do not achieve complete waterproofing
Precaution 1: The Texture and Color Rendition of the Printed Surface May Change
Since lamination involves applying a dedicated film over the base material, it has the drawback of altering the texture and color rendition of the printed surface. This is particularly true for glossy lamination, where the appearance of colors can easily change, so caution is advised.
If precise design reproduction and subtle color variations are important, we recommend including color proofing throughout the lamination process. This helps avoid the risk of costly reworks and ultimately leads to cost savings.
To avoid an outcome that does not match your expectations, it is important to take precautions in advance. The article below explains the necessity of color proofing and common pitfalls.
Seal Printing Color Proofing | A Crucial Process to Avoid Color Perception Issues
Precaution 2: Some Materials Are Not Suitable for Lamination
As mentioned earlier, lamination cannot be applied to all materials. It is not recommended for papers with distinctive textures (such as fine paper, Japanese paper, or craft paper) because it can compromise the texture and these materials are typically not chosen for environments that require lamination.
If you desire lamination, please consider the suitability of the material beforehand.
Precaution 3: Paper Materials Do Not Achieve Complete Waterproofing
Although lamination improves the water resistance and durability of seals, if the backing is made of paper, it will not be completely waterproof. While the film-covered surface is more water-repellent, it is difficult to prevent moisture from being absorbed through the adhesive side.
If exposed to water or left in humid conditions for an extended period, the lamination may peel off. For applications requiring complete waterproofing, such as outdoor or wet environments, choose film-based materials like Yupo or PVC.
Examples of Laminated Seals and Stickers
Here are examples of laminated seals and stickers produced by our company.
- Xplosion LLC Novelty Seals
- Note Inc. Novelty Seals
Case Study 1: Xplosion LLC Novelty Seals
We produced novelty seals for Xplosion LLC using glossy lamination.
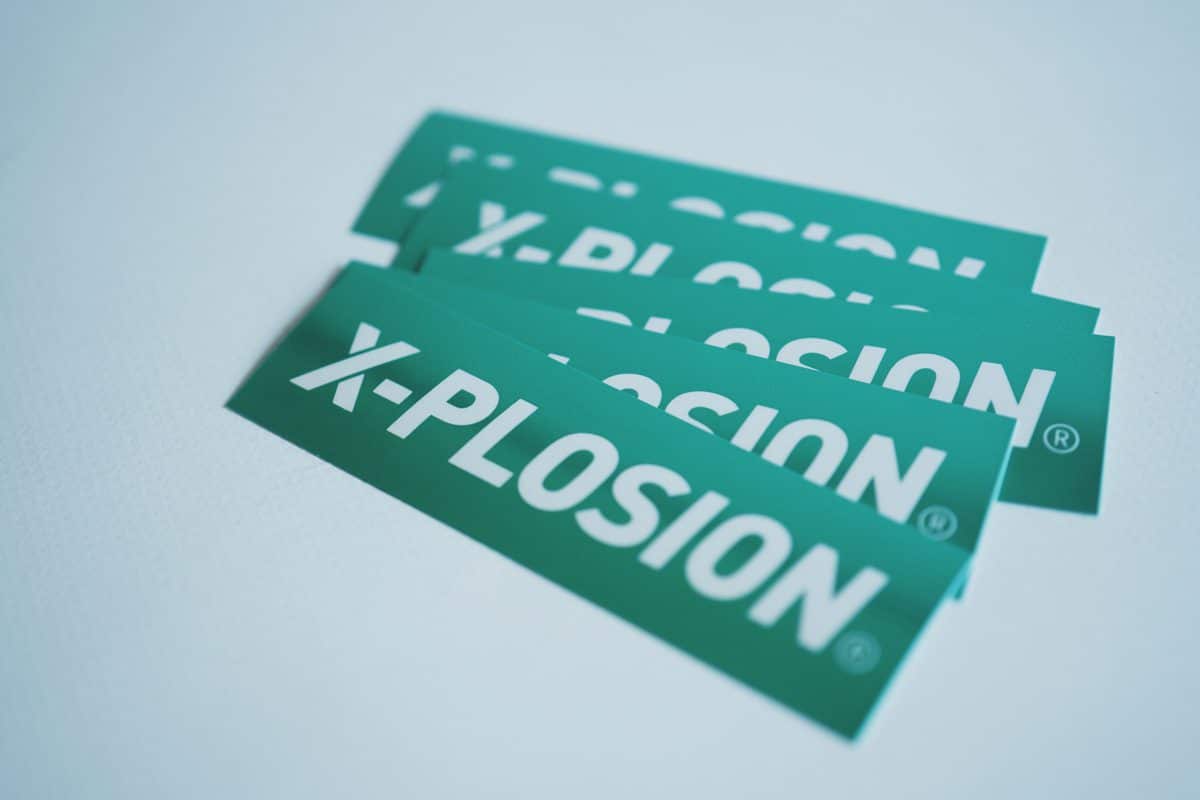
It is characterized by being protected with glossy lamination on a synthetic paper called Yupo, making it suitable for outdoor use. Incidentally, this seal is laminated over green foil to prevent the foil from wearing off due to friction. For example, when applied to a smartphone, contact with various items in a bag can cause the foil and ink to wear off more quickly. In such cases, lamination proves beneficial.
Case Study 2: freee Inc. Novelty Seals
We produced novelty seals for freee Inc.
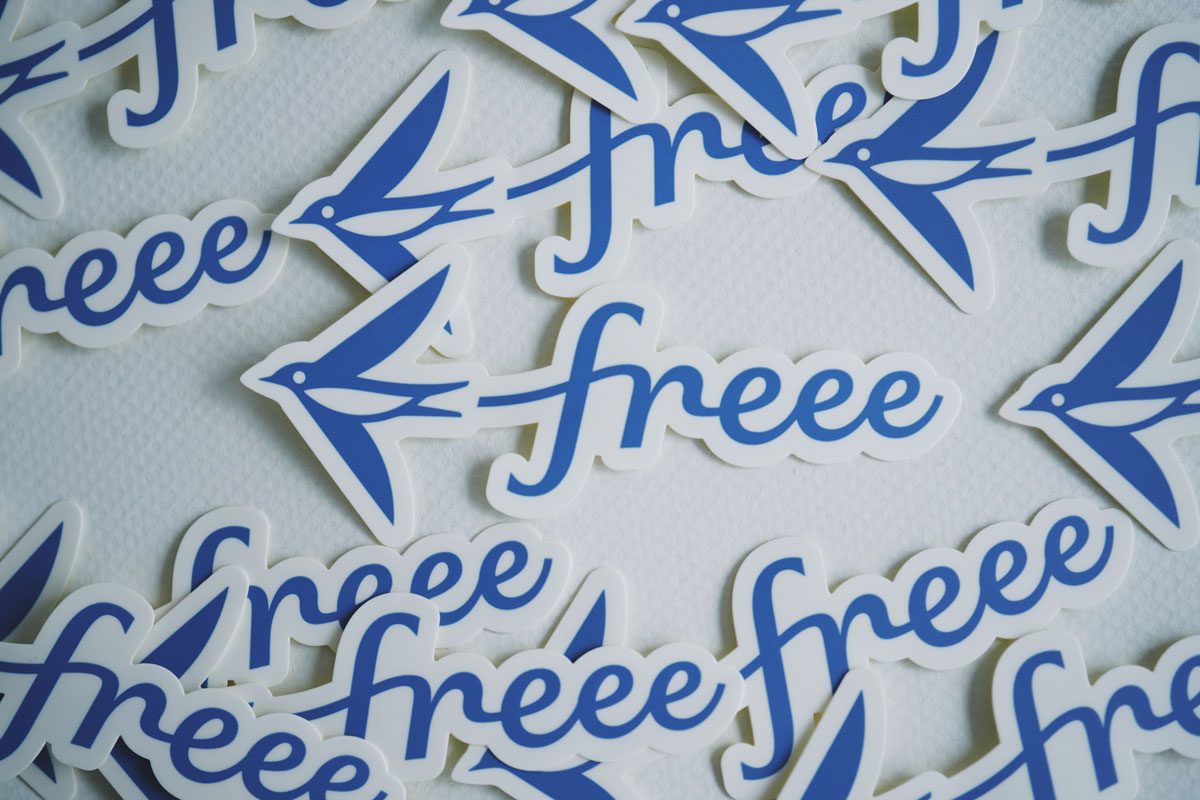
In this case as well, the seal was printed on Yupo and then applied with matte lamination. The matte finish provides a more luxurious feel compared to gloss, and it complements embossed logos well. Recipients are likely to be pleased to stick them on their notebooks.
If You Want to Apply Lamination to Seals or Stickers, Consult a Seal Printing Company
Lamination not only protects the surface of seals but also enhances their appearance. For seals used in demanding environments such as outdoors or wet areas, applying lamination for improved water resistance and durability provides peace of mind.
At our company, we carefully listen to your requirements during the quotation and consultation stages and propose materials and processing methods that match your desired outcome. If you are interested in discussing seal production in detail, please feel free to contact us.
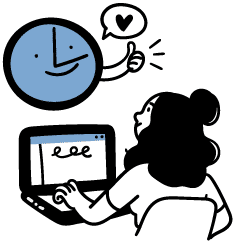
We provide same-day responses. Please give it a try.